By: Sarah Goltz, Content Manager on March 26th, 2021
Not ready to talk to a sales rep or copier technician yet? Here are some answers to your common copier questions
Content contributed by Jeff Spink, Director of Imaging Services
How much is a new copier?
There are a lot of variables that go into the price of a new copier, such as what manufacturer you are looking for and the extent of capabilities you require from your device. Some important things to think about before purchasing your new copier are the necessary features such as, do you require color or just black and white printing, the type of finishing (mechanical, chemical, protective coatings or laminated finishes), and what size or types of paper you will run. These kinds of variables will determine what cost you will pay for your copier. In order to find out the cost of your new copier, we recommend contacting a managed service provider to determine what copier is the best fit for your needs and budget. They will help deliver you a personalized solution for your copier needs.
Is my copier getting old?
Most copier leases are based on a 3-5 year lease. If it falls within that range and your objectives or print capacity on the machine does not, then the copier will continue to run well. Once seven years are up, some parts may become unavailable, and the machine will need more servicing and the reliability could decrease significantly. Also, if you use the machine over the suggested monthly volume recommendation, the machine might require more servicing to keep it running well. Most service contracts will also charge you overages if the contracted copy click amount is too high.
How do I know what size copier I need?
Usherwood sells and services a few different manufacturers, as well as many different models to fit your needs for your office. We sell small printers, mid-size copiers, light production, as well as full production machines. All these machines range in speed and volume tolerance. Our experienced sales department will give you a quote that will fit your needs according to a number of things such as number of prints and copies that you make monthly or what type of media you want to print on.
Are all copiers the same? What is the best copier you sell?
All copiers are not the same, some copiers have a speed of 30 pages per minute where others can be as fast as 150 pages per minute. It all depends on what you are looking to do as a customer. Choosing the best copier really depends on what you are looking for. The best solution for you is the one that meets your needs with room for growth. The speed, the reliability, the paper capacity, the document management solution, the security features, and a host of other variables go into answering this question. Our job is to ask the right questions so we can get clients the right copier. If we do our job correctly, our clients get the best copier every time.
I am getting lines on copies, scans, and sent faxes. How can I fix this?
When making copies and scans from the top feeder (automatic document feeder or ADF), the paper passes over a small piece of glass called the “slit glass.” This glass is on the left side of the main glass where you also make copies and is about an inch wide. Sometimes if you take your paper that came out with the lines and place it on the main glass next to the slit glass, you can match up the line to the spot on the slit glass to see where it needs cleaning. Sometimes you can even see the culprit right on the slit glass! The absolute best way to clean that glass is to use a Mr. Clean eraser if you have one, or a crumpled-up piece of printer paper! Scrub the slit glass and make a test copy or scan. Your line should now be gone!
Why does my copier say to load paper when it has paper in all the drawers?
Your printer or copier will say load paper if it does not have the proper size and type of paper that was sent from your computer in your print job.
Example #1
Let's say you print labels on your copier to the bypass tray, and your document was created in Word. You place the labels in the bypass tray, send the print, and it goes through and prints on your labels.
A week later, you use Word again to type a letter. You simply hit print and the copier tells you to load paper.
You look at every paper drawer in the copier and it has paper in all the drawers.
A closer look at the screen and it's actually asking for paper in the bypass tray. This can be because the last Word document you sent was to the bypass tray. Word remembers this and stays on the bypass tray even when you don't want it to go there. This particular setting is in Word.
Example #2
You send a legal-size print to your copier. If you have three, 8 1/2x 11 trays and one 11 x 17 tray, the machine will stop and say load paper. After a closer look you read the load paper screen says load paper "legal size."
The machine simply does not have the correct size paper to print your job. You can now delete the job, redirect it to another tray, or simply load legal size paper in one of your paper trays (adjusting side guides and tray settings when applicable).
Example #3
Another reason that it may say load paper is because you have the wrong kind of paper loaded into your print job. For example, if you set the copier to print on specialty paper but the copier only has standard paper loading inside of it, then it will display a message saying, “Out of Paper” or “Load Paper.”
Why does our copier jam after a long weekend or break?
A copier jamming after it has been sitting unused for some time can be due to the paper that is sitting in the trays. You may have had a perfectly good running machine all last week and all-day Friday.
The Holiday weekend comes along with Monday off and you return Tuesday, the machine can barely pass three to four pieces of paper without jamming. The machine did not mysteriously break while you were on vacation, the paper in the trays simply attracted moisture in the summer or completely dried out in the winter.
Extremely wet paper in the trays will not feed well and will curl up or roll up when it is dried by the machine's hot fuser unit. This curling up of the paper will cause jams no matter how big or expensive the machine.
In the wintertime, the same can occur, but because of just the opposite. Paper will dry out when there is low humidity in the air on a freezing cold winter day. Paper has a certain amount of moisture in it already, this moisture will dry out over a long weekend or holiday break or worst-case scenario even overnight. This will cause your paper to curl up to become wavy or warp. This causes jams on nearly any machine, big or small. To fix this remove any old paper that was in your machine and start with a fresh pack.
Read On
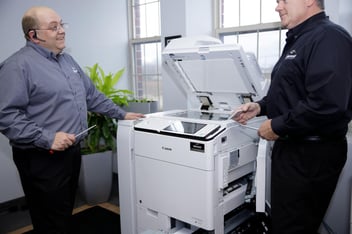
What to Review Before Replacing Your Old Copier
When making a purchase, you always want to feel secure and confident with your buying decision.
...
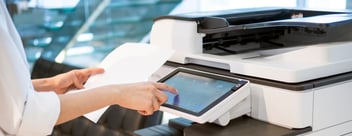
5 Best Copier Leasing Companies in the North Country
Finding the best managed printing services in Watertown, NY or the North Country can take time and...

3 Things to Review Before Purchasing a New Copier
Time to replace your old copier, but don’t know where to start? When you are thinking it's time to...